No products in the cart.
OUR PROCESS & CRAFTSMANSHIP
At D’Ophir, the making of each piece is a labor of precision, dedication, and mastery through our parent company, Ophir Textiles. Our process is rooted in the slow, intentional traditions of haute couture, where every fabric, stitch, and embellishment is carefully considered. We combine heritage craftsmanship with innovative techniques to create garments that transcend time
TECHNIQUE & ARTISTRY
Hand Embroidery
Hand embroidery is at the core of our designs, elevating each piece with intricate detailing. We employ a variety of embroidery techniques to bring depth, texture, and storytelling to our garments, including:
- Tambour Embroidery – A delicate, embroidery technique using a fine hook to create intricate beadwork and sequin patterns.
- Goldwork Embroidery – A technique using metallic threads and wires to create opulent, shimmering embellishments.
- Silk Thread Embroidery – A fine, precise method that allows for soft gradients and highly detailed motifs.
- 3D Embroidery – Raised embroidery techniques that create sculptural elements on fabric.
- Bead & Sequin Work – Hand-stitched embellishments using beads, pearls, and sequins to add dimension and light reflection.
Fabric Surface Treatments & Design
This category encompasses all the techniques used to alter and enhance fabric surfaces through dyeing, printing, and hand treatments.
Dyeing Techniques
Fabric dyeing is both an art and a science at D’Ophir. We employ traditional hand-dyeing techniques alongside modern approaches, ensuring rich, vibrant, and lasting hues. This process requires an understanding of fabric composition, temperature control, and color layering to achieve depth and complexity in every shade.
- Hand Dip-Dyeing – Layering colors to achieve ombré and gradient effects.
- Tie & Resist Dyeing – Techniques like shibori and batik that create intricate patterns.
- Natural Dyeing – Using plant-based and mineral dyes for organic, earthy tones.
Printing Technique
Our prints merge technology and handcraft for a balance of precision and uniqueness:
- Digital Printing – High-resolution imagery printed onto fabric with precise color placement.
- Block Printing – Hand-carved wooden blocks are used to create repeating patterns with texture, block printing involves hand-carved wooden blocks dipped in dye and stamped onto fabric in repeating patterns. This labor-intensive process ensures a rich, tactile quality that machines cannot replicate.
Fabric Manipulation & Marbling
From sculptural pleating to intricate ruching, we treat fabric as a medium for three-dimensional artistry. Through techniques such as smocking, gathering, and twisting, we create garments that have movement, volume, and dynamic texture.
- Pleating & Ruching – Folding fabric in structured or organic ways to add texture and volume.
- Smocking – Intricate gathering and stitching for stretch and texture.
- Fabric Marbling – Floating pigments on liquid surfaces to create organic, fluid patterns.
- Fabric Sculpting – Creating three-dimensional floral and abstract designs from fabric.
Ophir Signature Crystal Technology
Our innovation in textile embellishment is showcased in our Signature Crystal Technology, where crystals are meticulously placed on select fabrics at precise 1mm, 2mm, and 0.5mm distances. This creates a light-reflective surface that elevates fabrics to an ethereal brilliance. Notable pieces like the Lavender Dress from SS24 were crafted using this technique, demonstrating how science and craftsmanship merge to redefine luxury.
THE MAKING OF A D'OPHIR PIECE
Patterning & Draping
Each garment begins with an intricate pattern drafted by skilled artisans. We sculpt fabric on the form, allowing for natural movement and structure. Our draping process ensures that silhouettes feel fluid yet architectural, forming the foundation of every D’Ophir creation.
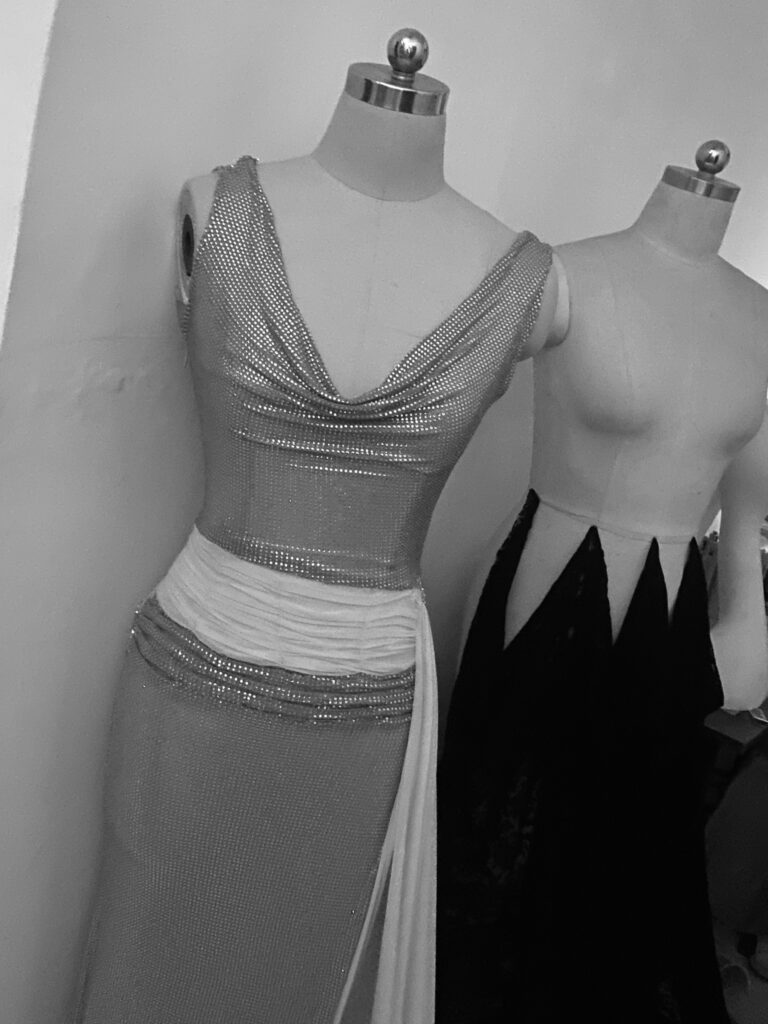
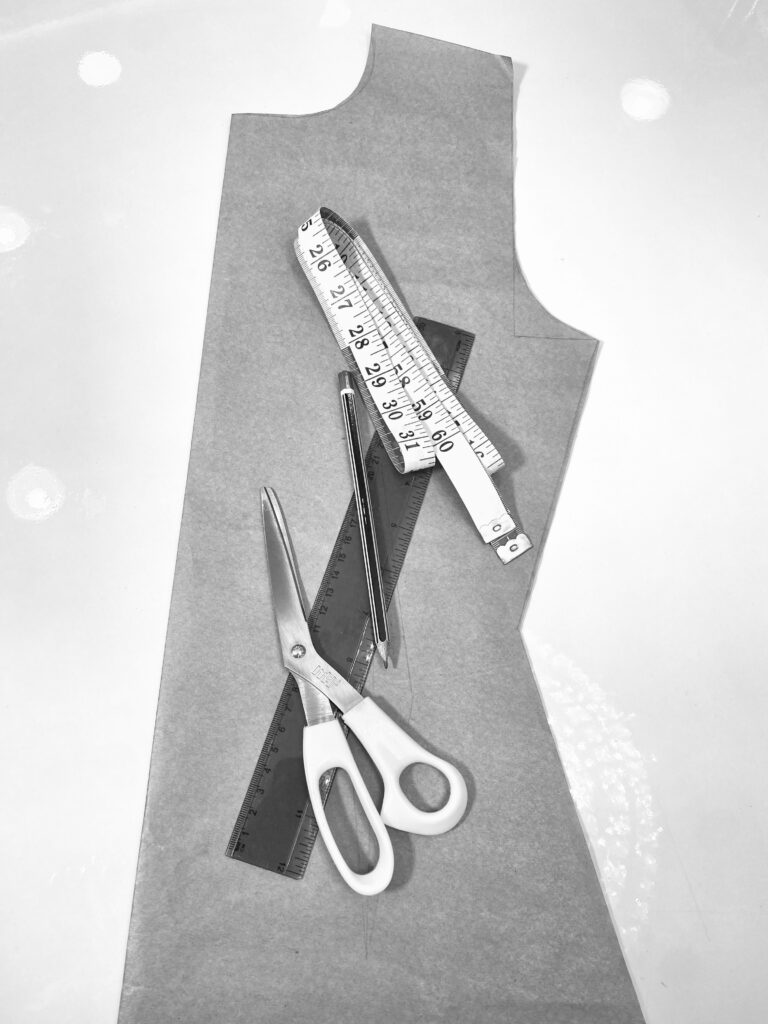
Sampling & Prototyping
Before a design reaches completion, we create multiple samples to refine fit, fabric choice, and construction. This iterative process allows us to perfect each detail, from seam placements to fabric layering, ensuring an impeccable final product.
Swatch Development
Every piece starts with swatch testing, where fabric combinations, embroidery techniques, and embellishments are experimented with to achieve the ideal aesthetic and functionality. This meticulous step ensures that each element harmonizes with the final design.
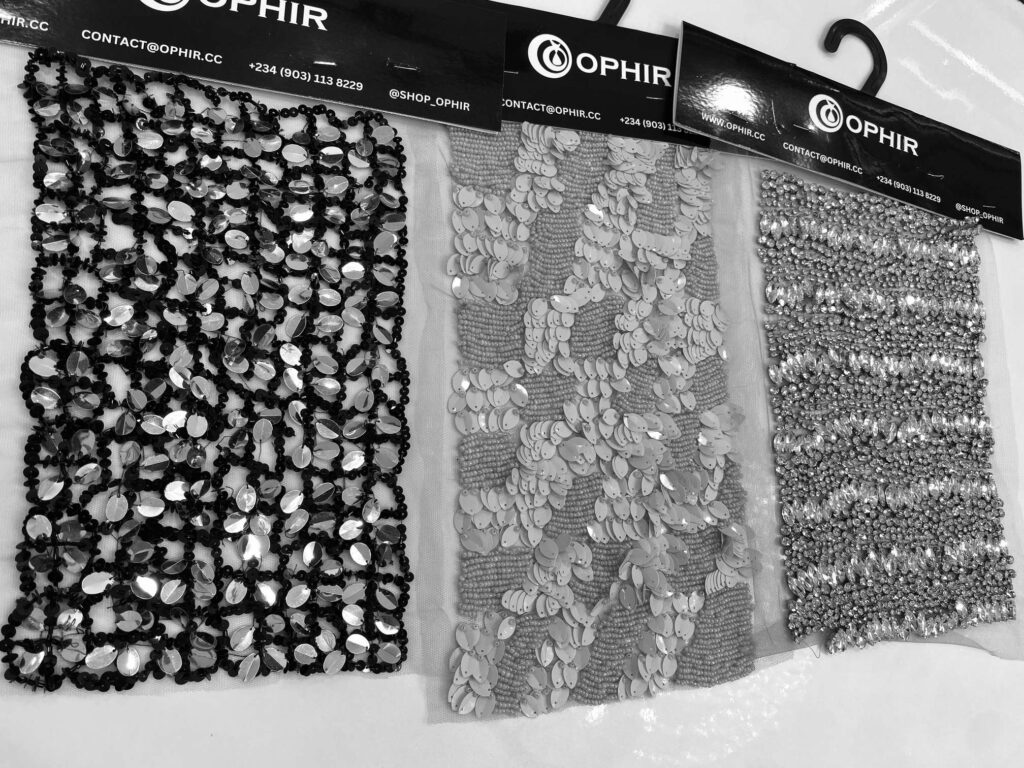
Stitching & Construction
Precision sewing and hand-finishing define the integrity of our garments. Our artisans meticulously stitch each seam, reinforcing delicate fabrics with traditional couture techniques such as French seams, hand-rolled hems, and invisible stitches. Every step ensures that a D’Ophir garment is as exquisite on the inside as it is on the outside.
Final Embellishments & Detailing
The last stage of the process involves delicate handwork, whether in the form of embroidery, beadwork, or crystal placement. Our embellishments are applied with precision, ensuring symmetry, balance, and flawless execution.
Finishing & Quality Control
Every garment undergoes a rigorous quality check before it leaves our atelier. Every detail is examined—every bead, every stitch, every hem—ensuring that the final piece is not just a garment, but a work of art.
At D’Ophir, our commitment to craftsmanship is unwavering. Each piece is a result of tireless dedication, skilled artistry, and an unyielding pursuit of perfection. From concept to completion, we honor the art of couture, creating garments that carry the weight of tradition while redefining the future of fashion.